How to Select the Right Engine-Driven Welder
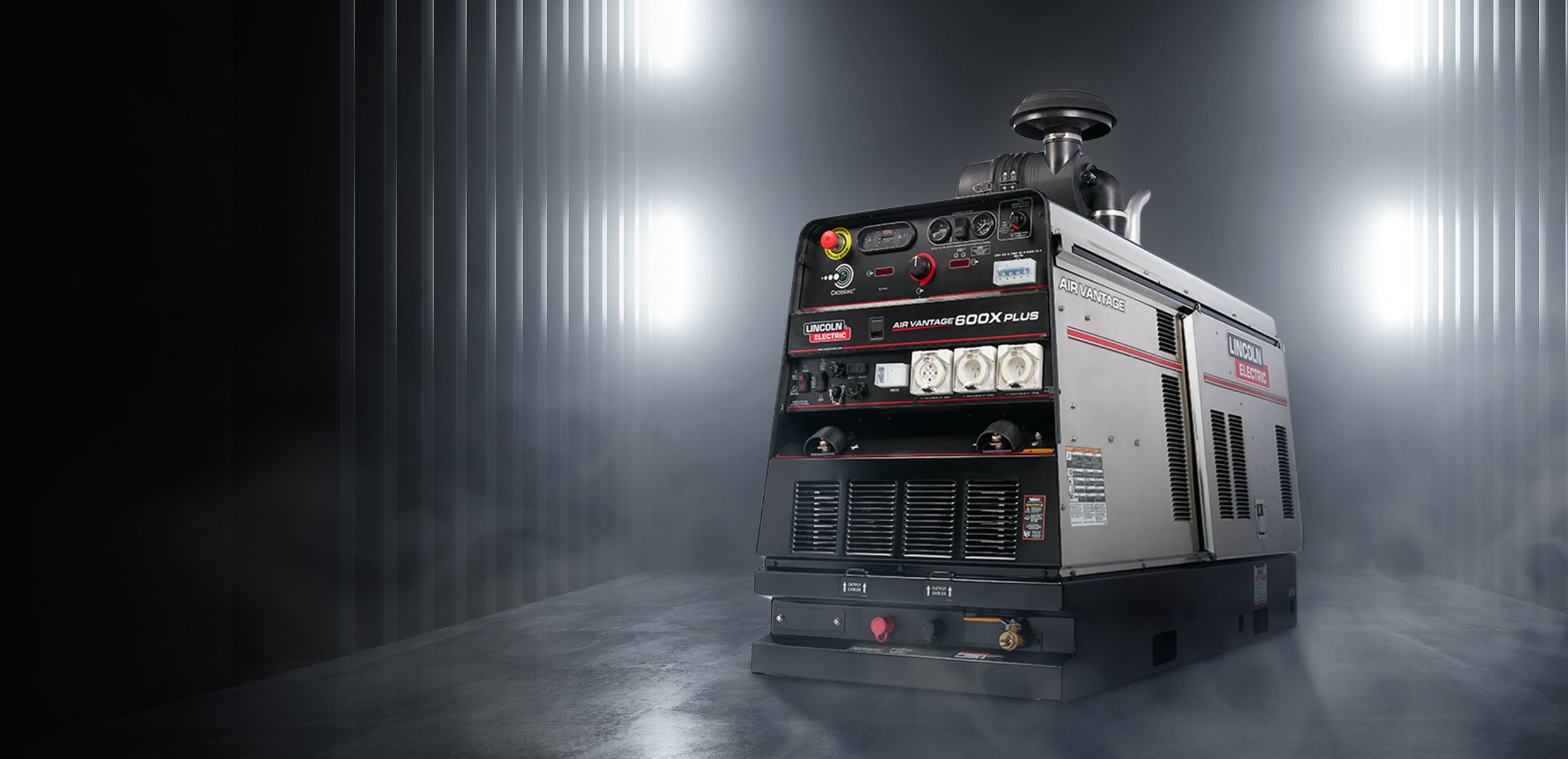
Engine-driven welders are generally used when electric power is not available for arc welding. Usually, these are outdoor applications. However, engine-drive welders are often used for indoor applications when it is not convenient to supply power to electric "plug-in" arc welders.
These indoor situations include everything from minor repair jobs to major plant shutdowns. When operating engine-driven welders indoors, vent the exhaust outside if at all possible, or use it in large spaces with good ventilation.
The basic considerations when choosing an engine-driven welder are:
- Application
- Engine Type
- Portability
- AC Generator Power
Application
In trying to select an engine drive, the first thing to consider is the application. Ask yourself these questions:
- Is this new construction or a repair job? Also, what is the size of the project?
- Is there a particular welding process you would like to use? You may want to stick with a process with which you feel most comfortable, or there may be a certain process required on the job.
- Is this a pipe welding project? The equipment chosen needs to produce an arc suitable for this type of work.
- Will the job require arc gouging? Arc gouging is repair work usually done in industrial jobs.
- What type of material needs to be welded? Most of the time the material will be a common mild steel plate. However, if it's aluminum, the welding will require different equipment.
Using this information, match it to the welding processes described below:
Process Descriptions
Stick Welding
CC (constant current) stick welding is the most common choice for fieldwork. Electrode (welding rod) diameters most commonly used are 3/32", 1/8" and 5/32". The simplest equipment will handle a wide variety of construction and repair applications. Output is measured in amps, and up to 200 amps is sufficient for the electrode sizes mentioned. Most equipment is DC (direct current) output for best arc stability. A 200-amp welder is usually able to get the job done.
Pipe Welding
Is most often done with stick electrodes. Look for equipment that specifies it will pipe weld, meaning that suitable arc characteristics are specifically provided for this process. Electrode diameters are typically 5/32" and 3/16", and 200 amps is sufficient for this process.
Arc Gouging
A process for removing metal. It is most commonly done in stick mode. An arc is used with a carbon rod to melt metal and compressed air blows the molten metal away. Gouging is used to remove bad welds and to repair cracks. Most operators use equipment with 400 to 600 amps for higher productivity with 5/16" or 3/8" diameter carbon rods. However, smaller rods can be used with lower amperage. For example, a 5/32" carbon rod can be used with 150 amps. Usually, a separate compressor supplies the air. A few engine-driven welders are manufactured with built-in compressors.
Wire Welding
CV (constant voltage) wire welding requires a wire feeder. Wire welding's main benefit is greater productivity: more weld metal can be deposited than for stick during the same amount of time. Although wire welding is much less common compared to the above processes, the application is growing. The engine-driven welder must have a CV-wire capability. Since most engine-driven welder work is outdoors, self-shielded flux-cored wire (which requires no shielding gas) is highly recommended to keep the process simple. When welding under windy conditions, the shielding gas associated with gas-shielded processes (solid wire or gas-shielded flux-cored wire) may be blown away, resulting in poor-quality welds. Output is measured in Volts and Amps. Wire diameters are typically .035" and .045", although 5/64" is often used for higher productivity. A welder with 30 volts and 300 amps is usually sufficient for many applications up to 5/64" wire.
TIG Welding
A slower, but more precise type of welding well-suited for thin materials and unusual alloys. A TIG torch and shielding gas are required. If welding on aluminum, an AC weld output is required from the engine-driven welder and a high-frequency generator is attached to start and sustain the arc. Or, an AC TIG welder can often be powered from the engine-driven welder's AC generator, if at least 8,000 watts is available. Most TIG welding is done below 100 amps.
Plasma Cutting
A metal cutting process that utilises an arc and compressed air. The engine-driven welder's AC generator can often supply power to a plasma cutter. At least 8,000 watts of power is recommended.
Air Vantage 600X Engine Driver Welder/Generator from Lincoln Electric
When the job calls for structural steel welding and other rugged outdoor work, you need an engine-driven welder that covers all your process needs – stick, MIG, TIG, flux-cored and gouging. The Air Vantage 600X has been re-engineered to deliver smoother arc characteristics and improved pipe welding capabilities and is Tier 4i compliant emission standard.
Choose the Air Vantage® 600X for 575A/43VDC 100% duty cycle welding and gouging with up to 10mm carbons. The Air Vantage® 600X includes a belt-driven VMAC® compressor with separate gauges to monitor compressor hours and pressure. Pulse welding capability for better arc control in out-of-position work and low heat input for critical welds.
A Superior Arc with a Superior Engine
Optimal arc performance
Take control of the arc and maximise the quality of your welds. The Air Vantage delivers the best arc in the industry with minimal spatter for stick or pipe welding. Expand your welding capabilities with customised modes for stainless, aluminium, steel and pulse welding.
Pulsing enables better arc control in out-of-position work and can lower heat input for critical welds. Enhanced gouging performance prevents the engine from stalling, resulting in smooth material removal.
Industrial diesel engine
• 4 cylinder 49kw turbocharged Deutz® TD2.9L4 diesel engine runs smooth and quiet.
• Standard engine gauges allow you to monitor performance at a glance.
• Tier 4i engine does not require ultra-low sulfur diesel fuel.
• 95 litre fuel tank for longer running time.
Low maintenance, reliable operations
The Air Vantage® 600X engine-driven welders contain less wiring and fewer connections than previous designs. The printed circuit boards are environmentally shielded using Lincoln Electric’s engineered encapsulation and protective frame trays. Standard stainless steel roof, side panels and engine-access door deliver excellent protection, durability and corrosion resistance from the elements.
Related Articles