Oil Filtration and Contamination Control for Ultimate Protection
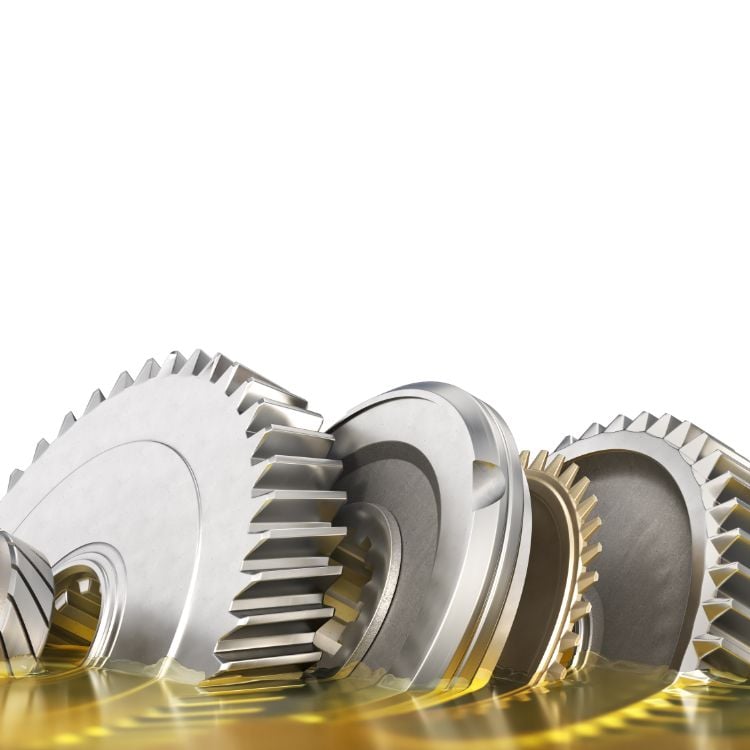
Contamination Handbook and fluid care Tools app
The Contamination Handbook and fluid care Tools app are resources designed to assist customers to remain on top of their fluid care, according to a HYDAC spokesperson.
The Tools app can be found on the top right-hand side of HYDAC’s homepage, with the app available for free download via Google Play Store or Apple App Store.
Once in, a customer can click on ‘Fluid Care’ for a wealth of information and tools to ensure optimum fluid cleanliness no matter the prevailing circumstances.
Oil classification, viscosity and contamination
Oil is classified according to API 1509 for base oils; DIN for hydraulic oils; and NSF International for food-grade oils.
Viscosity comparison is to ISO/SAE. The index according to ISO 2902 is based on a comparison of two mineral oils, with the higher the viscosity index of oil the smaller the change in viscosity in relation to temperature.
The causes and consequences of solid contamination, liquid contamination, and gel-like contamination in oil are delineated.
Solid contamination causes and consequences
For example, the causes of solid contamination could be installation contamination, ambient contamination, refilling of operating fluid, internal wear processes and oil ageing, with consequences including abrasive wear, increased leakage, component failure, control inaccuracies, blockage of control pistons, and short service life.
Liquid contamination causes and consequences
The causes of liquid contamination could be moisture from ambient air, leakage of cooling systems, process water/process steam, seal leakage, high-pressure cleaning, and chemical processes such as incineration, oxidation, and neutralisation. Consequences could include corrosion, reduction in dynamic viscosity that shows itself in a reduction in lubricating film thickness, contact with surfaces and wear, changes in oil properties that show up in the creation of acidic oil degradation products; formation of sludge, and an increase in speed of oil ageing, and cavitation damage.
Gel-like contamination causes and consequences
The causes of gel-like contamination could be oil aging and oil mixing. Consequences could include reduction in lubrication gaps caused by deposits that show in increased friction and temperature, increased bearing wear; malfunction in valves that shows in unstable control behaviour; damage to dynamic seals that show in leakage; blockage of filter elements that show in short filter life caused by sludge formation; and increased bearing temperature caused by caking.
Gaseous contamination causes and consequences
The causes of gaseous contamination could be mixtures and oil outgassing. Consequences could include cavitation; oxidation; and local overheating of oil in terms of an increase in the speed of oil ageing and control inaccuracies.
Solid contamination
Much focus is given in these resources on solid contamination in terms of cleanliness classes, cleanliness requirements, and photos/posters.
Cleanliness classes
Cleanliness classes are according to ISO 4406; SAE AS 4059; and NAS 1638.
In ISO 4406 particle counts are determined cumulatively, ie >4µm (c), ie >6µm (c) and ie >14µm (c) (manually by filtering the fluid through an analysis membrane or automatically using particle counters) and allocated to key figures.
Like ISO 4406, SAE AS 4059 describes particle concentrations in liquids. The analysis methods can be applied in the same manner as for ISO 4406 and NAS 1638.
The SAE cleanliness classes are based on particle size, particle number and particle size distribution. Particle size determined depends on the measurement process and calibration; consequently, the particle sizes are labelled with lletters A–F.
Like ISO 4406 and SAE AS 4059, NAS 1638 describes particle concentrations in liquids. Although NAS 1638 is no longer a valid industrial standard, it is often used in practice because of its simplicity (just one key figure).
The analysis methods can be applied in the same manner as ISO 4406.
In contrast to ISO 4406, certain particle size ranges are counted in NAS 1638 and attributed to key figures.
Cleanliness requirements
For system cleanliness of hydraulic and lube oil, the resources recommend using one class better than the cleanliness required for the most easily damaged component. As to filling/rinsing filtration, the resources recommend at least one filtration rating finer than the system filter. According to DIN 51524 a cleanliness of ISO 21/19/16 must be provided for fresh hydraulic fluid.
For diesel, the ISO 4406 target cleanliness class for tanks is 18/16/13 at a filtration rating of 5µm (single pass elements), and the class for injection systems is 12/10/8 at a filtration rating of 5µm (single pass elements).
Photos/poster
The Tools app provides photos/posters of ISO 4406 (Class 14/12/9, 15/13/10, 16/14/11, 17/15/12, 18/16/13, 19/17/14, 20/18/15, 21/19/16, 22/20/17, 23/21/18); SAE AS 4059 (Class 4 to 13); NAS 1638 (Class 3 to 12); and an ISO 4406 cleanliness poster.
The Contamination Handbook provides many photographs and illustrations to reinforce written information.
Liquid contamination
Focus is also given in these resources on liquid contamination in terms of water in oil saturation and the saturation limit of water in oil. In addition, information is given on water saturation curves of different oils in parts per million and the life expectancy of bearings in relation to water content.
Gel-like contamination
In addition to solid and liquid contamination, gel-like contamination also has to be contended against in terms of membrane patch colorimetry and particle measurement varnish analyses.
The idea behind it is that the colour of hydraulic and lubricating oils will change as they oxidise and age. This is due to build-up of damaged and degraded elements in the oil.
Varnish in oil causes untold problems in systems, such as sticking control valves and other operational problems, increased temperatures on bearing, decreased heat transfer in coolers, increased filter element consumption, and decreased oil lifetime.
By analysing this colour change HYDAC can check the level of varnish present in the oil and assign a number to the colour in order to quantify and report on its condition. This method is called membrane patch colorimetry or MPC.
As to particle measurement, it takes place at 20°C and 80°C based on ISO 11500.
For more in-depth information the tools app features editorial on varnish in turbine oils and videos on how to use a varnish elimination unit and a MPC field test unit and how to efficiently eliminate varnish from a hydraulic system.
Gaseous contamination
Gaseous contamination in air or oil is also given its due attention in terms of the solubility of air in oil, cavitation, and air-release capacity.