What engine drive is right for your service truck/trailer?
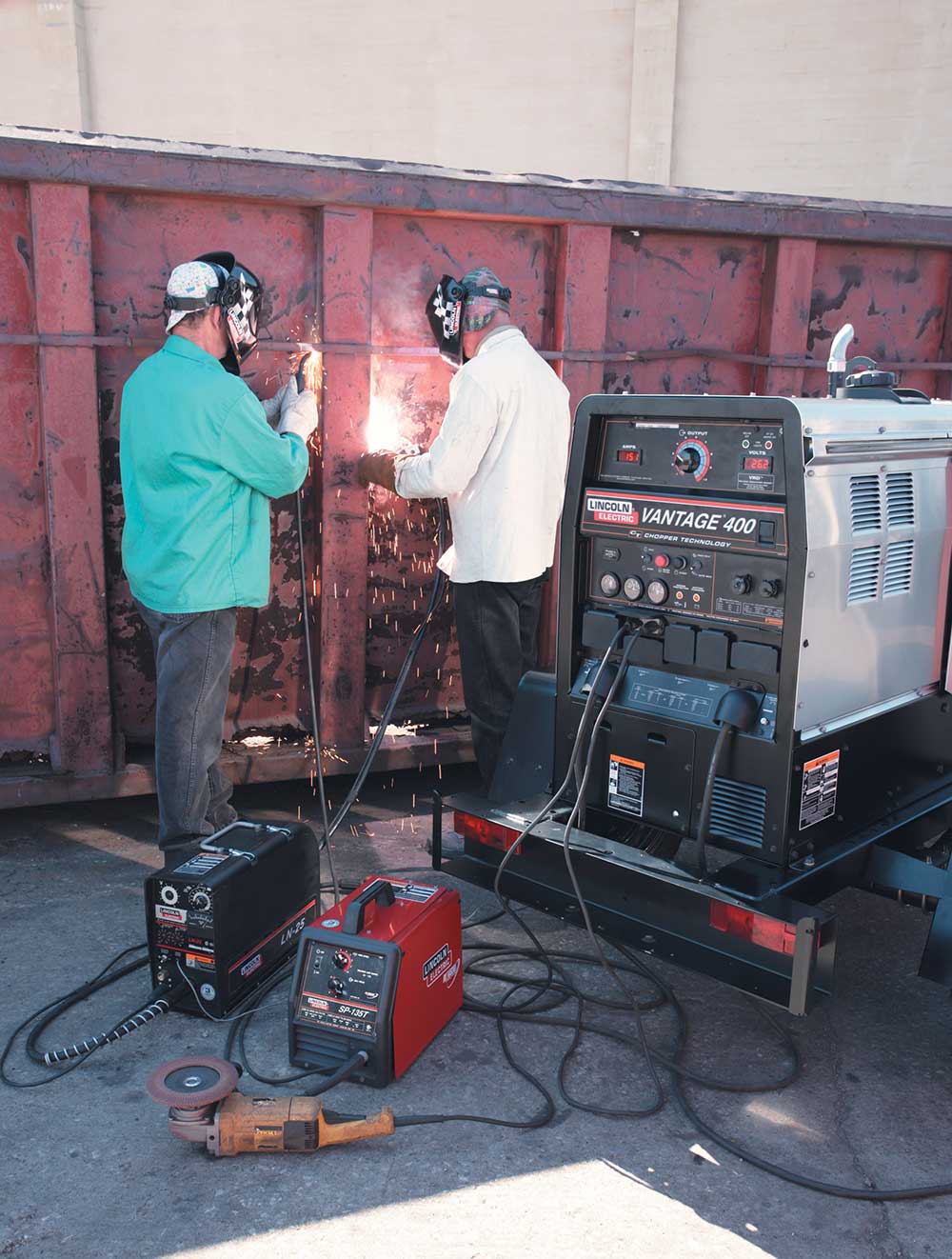
SHOP BRAND |
If your job takes you out of the workshop and into the field, it’s likely that an engine-driven welder is an important component in your overall arsenal of equipment within a mobile service truck or trailer.
Engine-driven welders are generally used when electric power is not available for arc welding. Usually, these are outdoor applications. However, engine-drive welders are often used for indoor applications when it is not convenient to supply power to electric "plug-in" arc welders.
These indoor situations include everything from minor repair jobs to major plant shutdowns. When operating engine-driven welders indoors, vent the exhaust outside if at all possible, or use it in large spaces with good ventilation.
Of course, with so many engine driven options in the market, it can be hard to know which one is best for you and your specific applications and needs when fitting it out.
There are many factors to consider – truck/trailer size, weight, fuel type, power requirements and more.
Truck/trailer size: What is the available space & weight restrictions of your truck or trailer? Remember you need to keep it in the context of the various other pieces of equipment that you’ll be storing and transporting in that same space.
Fuel: What type of fuel do you need? The answer is directly connected to power output and size and weight considerations. Diesel engine drives operate will be on the higher end of the power output spectrum – 300-450 amps or more. This heavier, higher-output equipment is also where the multi-function units are more prevalent. Machines in this output range tend to be lighter in weight and smaller in footprint, which could make them the more fuel- and space-efficient option for your truck and truck bed.
Sound: Some engine-driven elders run quieter than others, due to a variety of factors: size, power output, design, built-in noise-insulation features and more. Noise reduction can be a workplace requirements for two reasons: work environment and worker safety.
Quieter residential areas may have more restrictions related to noise, while industrial environments or remote locations will likely have fewer if any such restrictions. However, in both cases, a quieter machine can improve communication for workers positioned near the machine. In addition, decibel levels past a certain threshold will warrant hearing protection for the operator according to Workplace Safety regulations.
Power Requirements
The discussion of power requirements in engine-driven welders hinges on two basic factors: welding output and generator output.
Welding output: Consider what you’ll be welding with this machine, and what your go-to process in the field will be. Will you be doing larger and more demanding jobs or will you be doing smaller jobs related to maintenance and repair? If you intend to remain primarily in stick welding, 200 amps will be sufficient output. If you’re thinking of a wire process or gouging, you’re more likely to operate in the 300-450Amp range
Engine drives are also frequently used for arc gouging. The larger the carbon rod, the more welding output is necessary. For example, 10mm carbon rod will require a 400-amp machine.
Generator output: The discussion of generator output starts with the question: “What am I running in addition to the welder itself?”
Engine-driven welders generate auxiliary (AC) power that can be used to run lights, pumps, power tools and other devices – including additional welders or plasma cutters. More refined output power – often referred to as clean auxiliary power – enables the user to run sensitive electronic equipment. This clean power feature is available on Lincoln Electric’s Vantage 400 units.
The typical components on a service truck/trailer include an air compressor, a crane and a welder/generator. Depending on your array of components and their combined power demands, you may need anywhere from 5,000 to 10,000 watts of generator output power, and possibly more depending on your anticipated applications. Key considerations of Generator Output when selecting an Engine Driven Welder include:
Peak power vs continuous power: The peak power will always be higher than continuous power, but can only be sustained for a short time (about 30 seconds or less). Peak power is needed for certain applications, such as starting pumps or other inductive loads, which can require a large in-rush current to get running. After that initial surge, it settles into the lower, continuous power rating. Continuous power is the power available at a 100% duty cycle.
Always be sure you are comparing peak ratings to peak ratings and continuous rating to continuous ratings.
Single phase vs three phase: Single- and three-phase auxiliary power are fundamentally different due to the design of the AC circuit. As a result, these two types of output cannot be directly compared. More importantly, jobsite tools may require one over the other. For example, most hand-held tools are single-phase, while many pumps, welders and plasma cutters require three-phase power. Furthermore, the available three-phase power will be higher than the available single-phase power.
Once again, be certain to compare available three-phase with three-phase, and single-phase with single-phase.
Simultaneous welding and auxiliary power: Just like the weld output ratings, the auxiliary power ratings are the maximum output the machine can give you. These machines are designed to provide both auxiliary and weld output at the same time, but there is some give and take. When you increase the weld output the available auxiliary power decreases, and vice versa.
Reliability/Peace of Mind
Your experience with an engine-driven welder extends well beyond the initial purchase process. Look for a product whose manufacturer has a presence in your area and provides optimal support in terms of warranty, maintenance and service.
Most machines are covered by two warranties, one on the welding side and the other on the engine side. It’s important to understand the parameters of both.
The Lincoln Electric Vantage® 400 compact 400 amp engine-driven welder/generators is the ideal machine to be used on a mobile service truck/trailer. Compact enough to fit on small to medium truck/trailers to aid in flexibility of use yet powerful enough for most job requirements – even arc gouging.
- It’s also one of the quietest, with a smooth-running, 4-cylinder Perkins® diesel engine.
- Use this multi-process welder for arc gouging with up to 8mm carbons, stick weld with up to 6mm electrodes and CV wire weld with up to 2.4mm wire.
- Superior arc performance delivered by Lincoln Chopper Technology® ensures optimum productivity.
- You’ll also appreciate the VRD (Voltage Reduction Device), which reduces OCV (open circuit voltage) in the CC-Stick weld mode for added safety.
- This model efficiently generates 13,200 watts of AC generator power for your lights, grinders and power tools.
- Housed in a rugged, low-maintenance stainless steel enclosure, it’s loaded with many innovative service features.
It’s a power package that’s excellent value and is ideal for use in general fabrication, general maintenance/ repair and construction sites.
Remember to always weld safely by wearing an acceptable eye protection (1/1/1/1 optical clarity) in your Welding Helmet, suitable Welding Jacket & Gloves for the welding process that you are performing.