Smooth Concreting with High-Precision SikaGrout® 212 HP
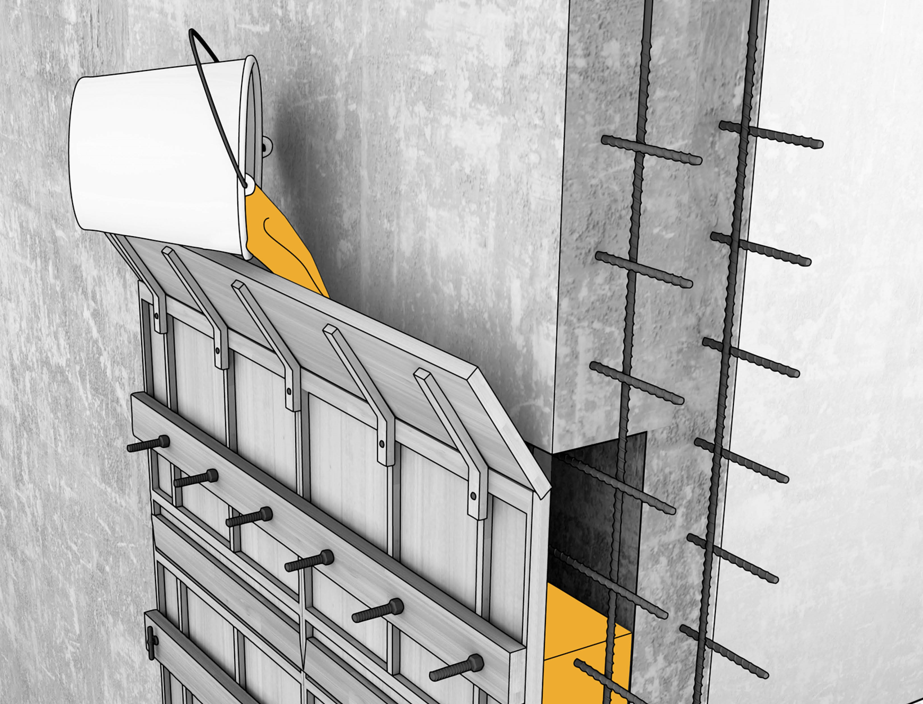
Concrete grouts can often shrink and crack after drying and curing, especially if conditions aren’t optimal during the mixing process! SikaGrout, developed by Swiss chemical company Sika Corporation, helps overcome some of these challenges, containing additives that lower the risk of cracking and shrinking.
SikaGrout is specifically engineered for structural applications across the construction, mining, infrastructure and motor industries. This includes SikaGrout® 212 HP – a non-shrinkage, high-performance, Class C cementitious grouting.
Applications and benefits
SikaGrout® 212 HP is used for filling gaps, voids and cavities in structural components, transferring loads, anchoring and fixing non-structural elements. The product is suitable for grouting applications in residential and commercial construction and heavy industry.
Features and benefits include:
- Shrinkage compensation – made with an expansive component that offsets drying shrinkage, making it a high-precision product. This feature reduces the risk of volume changes and cracking.
- Easy-handling – premixed mortar where you just need to add water and stir.
- Easy to apply – a free-flowing product that can be either pumped or poured.
- Versatile – use it to grout column base plates or machine bases, enlarge elements, anchor bolts, fix posts.
- High consistency – avoids the segregation and bleeding problems that can lead to increased porosity and reduced strength.
- Excellent bonding and strength – includes fast strength development, and high impact and thermal resistance.
- Non-corrosive – does not corrode steel or iron.
Instructions for use
Using SikaGrout® 212 HP correctly is crucial to ensure the product works as it should, as incorrect mixing or usage could result in structural problems or failures.
To prepare and use:
- Prepare the substrate, ensuring it is clean and free of dust, debris or other contamination.
- Pre-wet the substrate surface.
- To start the mixing process, pour the minimum recommended water ratio into your mixing container.
- Add the grouting powder bit-by-bit while mixing with a mechanical mixer at low speed.
- Add more water to achieve the desired consistency, but never exceed the maximum amount.
- Mix for three minutes until it is homogenous.
- Depending on the method you are using, pour or pump the grout with suitable tools or equipment.
- Throughout the process ensure the grouting area is always confined.
- Cure for a minimum of three days.
Temperature can affect the setting time and strength development of the grouting mixture. Optimum performance occurs between 18 and 25 degrees Celsius – which applies prior to and during application and for 48 hours afterwards.
Handy tips for a great result
Resty Briones, Technical Support Engineer at Sika Australia, says careful and correct substrate preparation and mixing are essential for good results. “Resist the temptation to water down the grouting mix in order to stretch it out,” he says. “Doing this only reduces the product’s strength and could in turn lead to cracking and failure.” Resty says the product can be cooled down in summer by using ice and cold water, or warmed in winter with heated water. “It’s important to ensure the mixture isn’t exposed to rain for at least eight hours,” he says. “Proper curing is essential, especially during summer to avoid evaporation.”
SikaGrout® 212 HP – is high precision, like a Swiss watch! Find the product and others in the Sika range at Blackwoods online.