Inspection of Pressure Vessels: One Tricky Business
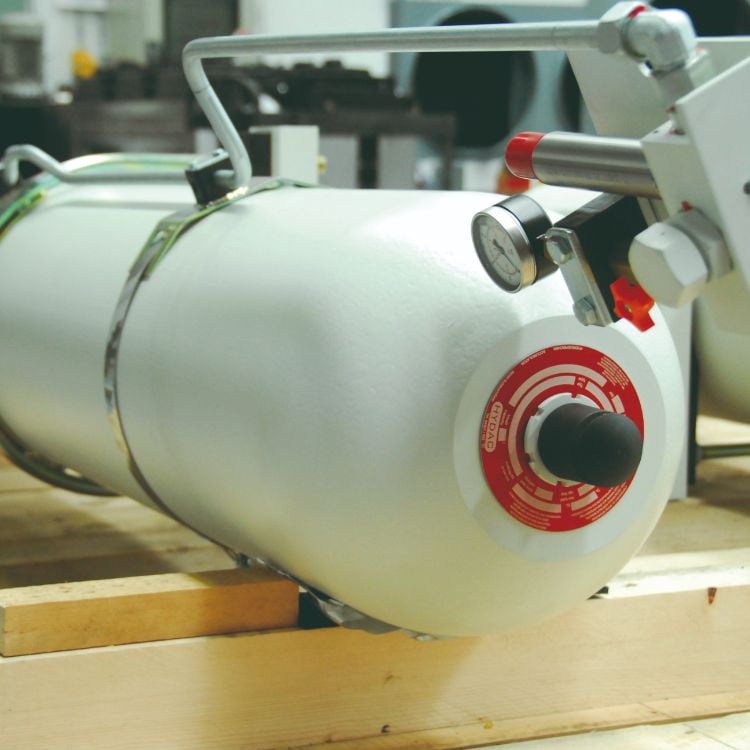
Pressure vessels in Australia are backed by a comprehensively researched set of legislative documents and mandated inspections that must be heeded to protect the populace.
These put the onus on a pressure vessel’s owner to comply with design registration and ‘item of the plant’ regulations.
In addition, they have to have a management system in place to ensure the continuing integrity and safety of pressure equipment. This entails full control over the pressure vessel’s documentation spanning all information from design registration and the manufacturer’s data report to drawings and vessel location.
This documentation has to be readily available to a WorkSafe inspector or representative as well as inspection documents. Inspection documents are concerned with a number of different standards, particularly AS 3788, which sets out the requirements for in-service pressure vessel inspections.
These inspections centre around a number of different inspections on a particular plan, with the owner obligated to keep a record of these inspections as part of the documentation.
Inspection requirements: AS 3788 for scheduling inspections
AS 3788 sets out inspection requirements in terms of when inspections have to be undertaken – quite a number at different intervals and occasions – and who is authorised to conduct them.
Commissioning inspection:
Before pressing a pressure vessel’s start button, a commissioning inspection focused on procedure has to be undertaken.
This is because before a hydraulic accumulator gets to a plant many things could take place from the accumulator getting a dent or a falling object gouging it to rusting occurring due to weather conditions.
The commissioning inspector takes a look at the procedure, which includes ensuring the integrity of the vessel and that it is fit for its intended application.
This isn’t applicable to hydraulic accumulators because they’re typically mounted onto hydraulic systems but rather to larger pressure vessels such as boilers or air receivers.
Periodic inspection:
Following this are periodic inspections once the vessel is in place and operational to ensure its integrity.
Inspection following excursion or damage:
Inspections following excursions or damage to the vessel are necessary to ensure the integrity of a vessel after it’s been exposed to a fire in a refinery or flooding in a factory that has caused rusting and corrosion across different items of the plant, as examples.
Inspection for proposed change process in service condition:
This inspection is to ensure a vessel is suitable for a proposed change process in service condition such as if a hydraulic accumulator’s medium is to change from hydraulic fluid to water. This is because water has a corrosive nature, which can impact the health of the business.
Inspection following repair alteration:
Owners are obliged to comply with the inspection following repair alteration as indicated by AS 3788 from a regulatory point of view. This entails a procedure inspector signs off that a vessel is fit for purpose following repair work.
Examples include a pressure vessel that has some gouge or some corrosion on an internal surface and repair work is done to clear the corrosion and paint the vessel or weld a supporting plate around the gouge, as examples.
Inspection of idle equipment:
Inspection of idle equipment pertains to a plant that has been put into idle mode for six months, as an example, with a particular pressure vessel such as an
air receiver remaining dormant. Over that period corrosion-causing condensation could take place in the receiver, which could render it unfit for purpose.
Note that damage to the air receiver would have been a passive process, which highlights how important it is that the owner keep an eye on idle equipment and takes any preserving actions to maintain a vessel’s integrity.
Inspection for remaining life of a pressure vessel:
The inspection for remaining life of a pressure vessel pertains to the duration of time the vessel will remain fit for purpose.
Some corrosion is permitted on a pressure vessel’s external walls. However, as the corrosion occurs, the vessel’s remaining life starts to shorten.
Therefore it’s important that owners keep an eye on their vessels, including the rate of corrosion, in order to have an accurate idea as to how long the vessel can be operational without any catastrophic failures.
Periodic inspections:
Even if an accumulator is in service and operating well it still has to undergo periodic inspections as stipulated in AS 3788’s Table 4.
Table 4 informs as to what inspections have to take place for different vessels.
Point 10.1 in Table 4 suggests inspection regimes for different pressure and volume, with a specified interval for a PV value – the result of multiplying pressure in volume – between 100 and 200MPaL, and a different specified interval for a PV value greater than 200MPaL, as examples.
A 50L hydraulic accumulator (most relevant to the fluid power industry) with a design pressure of 400 bar would have a PV value greater than 200MPaL.
Table 4 indicates that a commissioning inspection is required and a first yearly inspection, which is both an external and internal inspection of the vessel.
Furthermore, it specifies that external inspections have to be undertaken every second year, with each inspection accompanied by its own report system and documentation.
As to internal inspections, they have to be undertaken every 12 years.
Under certain circumstance they can be exempted or inspection intervals can be extended for a certain number of years.
This is especially of interest to customers in that they always want to know if they can mitigate or postpose inspections.
The answer to that is that that the 12-year internal inspection where the vessel is pulled apart can’t be avoided, but the first yearly inspection applicable to pressure vessels starting from small one-litre accumulators to multi-megawatt boilers or huge air receivers and larger items can be mitigated when the owner is 100 per cent sure that the pressure vessel in question is intact after a year and will remain intact for the next decade.
Risk-based inspection:
There the standard suggests a risk-based inspection, which is an alternative to inspections listed under Table 4 in AS 3788.
In a nutshell it’s all about understanding the risks associated with bearing the integrals identified in that particular table.
The process of a risk-based inspection involves first and foremost that the stakeholders in a pressure vessel from the owner and inspector to the engineers, maintenance manager and operation manager are in agreement to undertake this alternative inspection.
This entails preparation of a risk assessment and management of documentation to justify a variation on the routine inspection stipulated by the standard. It also entails taking a look at the risk of not running an internal inspection in the first year in terms of what could potentially go wrong, the severity of risk, potential impact on a plant and whether, in fact, there is a particular process detrimental to the life of a pressure vessel.
Agreement from stakeholders is necessary because scenarios can evolve where the maintenance team says it doesn’t mind if something goes wrong after completing the risk assessment in that it doesn’t believe there is any risk to health or life and that it is able to make necessary replacements. Then the operation manager chimes in that maintenance team may have a spare that can be swapped over without any problem but that his department has concerns as to the financial damage of the plant shutting down. The health and safety manager could exacerbate the matter by pointing out that the standard cannot be overruled because that could have an impact of the life of a person and the health of a property – and so it goes.
However, if there is agreement that the integrity of the plant is not compromised then the internal inspection can be overruled. This also includes buy-in from the inspector contracted to inspect the plant.
HYDAC International is a world leader in motion control and fluid technology, operating in over 50 countries with over 9,000 employees and 500 sales and service partners worldwide.
HYDAC offers an extensive product range to cover all areas of fluid power. The company also provides on-site reliability audit program, cleanliness solutions for oil and fuel, calibration services, engineering advice, bespoke design and drawings, hydraulic services, technical training and predictive maintenance / Industrie 4.0 solutions.