Managing the Risks of Welding Fumes
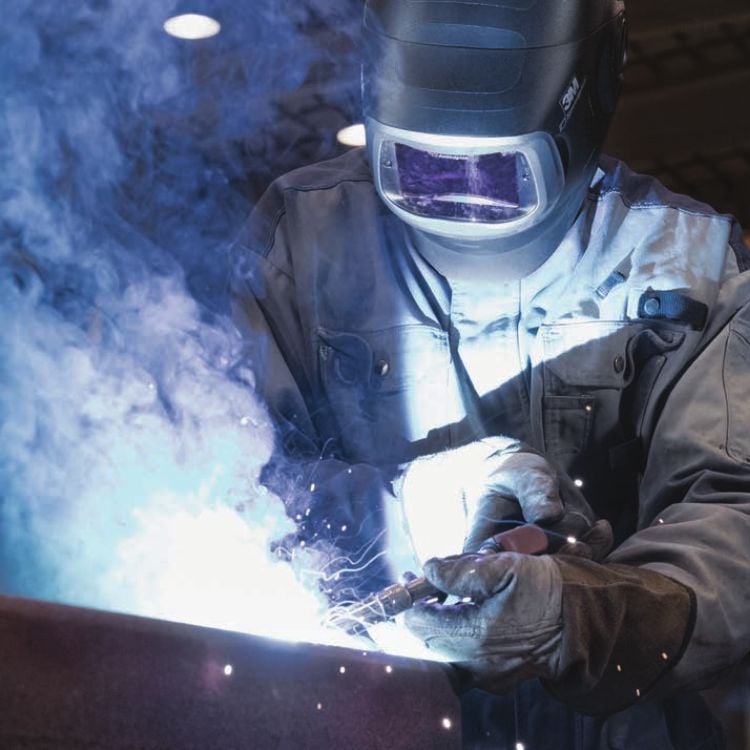
Take a look at this list: cancer (lung, larynx and urinary tract), bronchitis, pneumonia, asthma, emphysema, skin disease, and damage to the central nervous system and kidneys. These are some of the health issues that can arise if someone is exposed to welding fume.
Whilst welding is a task performed across many industries and can be inadvertently overlooked, the reality and gravity of these health issues was underlined in 2017 when the International Agency for Research on Cancer (IARC), re-classified all welding fume generated from welding as ‘Carcinogenic to humans.’ Put simply, welding can be a hazardous occupation if you are not suitably protected, and appropriate safety practices are not adhered to. An inherent challenge with the above is that some of these health issues may not arise for many, many years.
In Australia, there are exposure standards to contaminants. The standard for general welding fume, which is measured
inside the welder’s helmet when worn (‘breathing zone’), must not exceed 5mg/m3 using a Time Weighted Average
(TWA) of eight hours per day over a five-day working week; this excludes other fume types such as chromium and
copper which are lower.
“The understanding of safe practices and obligations associated with welding fume continues to improve in Australia. Over the last 24 months alone, we’ve seen a significant lift in enquiries from safety advisors, production managers, workshop leaders and the like on Welding PAPR (Powered Air Purifying Respirators), welding fume controlling systems as well as the associated PPE,” says Dino Paris, Blackwoods Technical Specialist Team Leader, Welding, Gas & Abrasives. In support of these enquiries, many customers enlist the involvement of the combined Blackwoods technical safety and welding, gas & abrasives teams for industry best practice guidance. Through onsite assessments our team of experts enable customers to conduct hygiene assessments that provide them with peace of mind, or an applicable and practical fit for purpose solution. When providing onsite assessments, the five-tier Hierarchy of Controls methodology is applied:
1. Elimination: Remove the hazard (fume).
2. Substitution: Replace the hazard.
3. Engineering controls: Isolate the hazard by maintaining designating (welding) areas and minimise or remove fume
through controls.
4. Administrative: Change the process, consider shift rotations and position workers to minimise or remove exposure to fume.
5. Personal Protective Equipment (PPE): Use appropriate protective clothing and respiratory equipment. The controls are listed in order from the most to the least effective. In almost all situations, a combination of these controls is needed to best protect welders.
The Blackwoods team of technical specialists are available to assist you in undertaking a hygiene assessment for peace
of mind, or to assist in identifying a tailored solution to keep welders safe.
Get in touch with your local Welding Specialist today.