Improve Welds with Twin-Wire Welding Advances
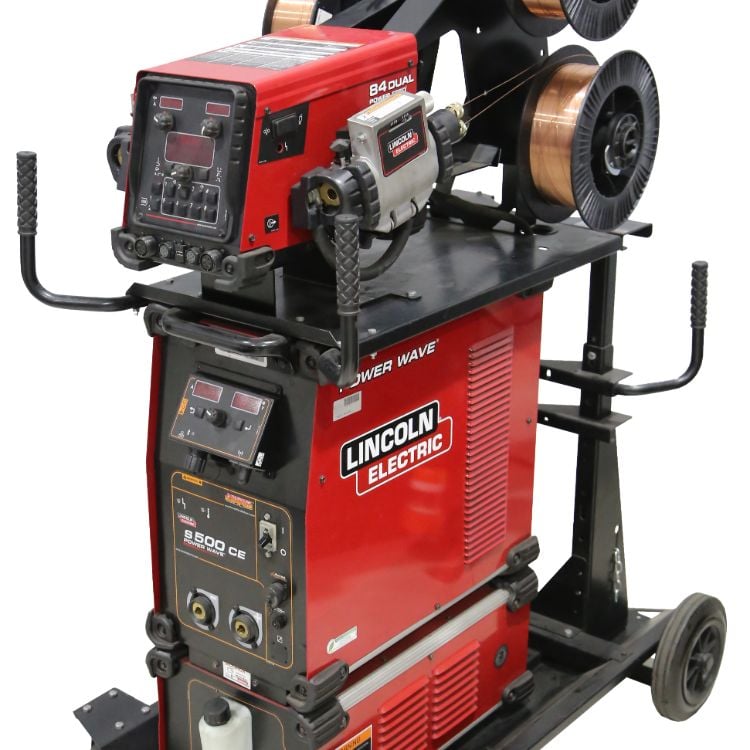
The skilled worker shortage, labor and material costs, as well as the complexities involved with adopting new technology, are among the biggest pain points for manufacturers.
But when production calls for larger-sized welds on thicker metals, these issues can be exponentially problematic. In these applications, operations that rely on traditional single-wire or complex tandem welding processes risk efficiency losses that can have long-term impact on their bottom line. Fortunately, advancements in twin-wire welding – specifically the patented Lincoln Electric HyperFill® twin-wire process – have made it possible to achieve higher levels of productivity while eliminating or reducing the impact of these common challenges.
The Challenge
Welding thicker materials using traditional single-wire processes tests the abilities of a manufacturer’s welding workforce and budget. Because these applications call for larger welds, requiring more filler metal and multiple passes, controlling costs can be a substantial undertaking for operations already facing the following challenges:Skilled Labor Shortages
The skilled-employee shortage is a major problem for many manufacturers. At one point, 40% of manufacturing companies declined new contractsbecause not enough skilled workers were available, according to the American Welding Society.1 Achieving high deposition welding efficiently using single-wire processes requires highly skilled welders. When elevated wire-feed speeds are used, controlling the welding puddle can be difficult for the average welder. This is why many operations struggle to achieve higher levels of productivity.
Labor and Material Cost
As the cost of welding labor and materials goes up, so does the need to conserve those resources. When done properly, high deposition welding can reduce unnecessary rework and allocate labor more efficiently, resulting in increased savings.Sources of common welding production expenses include:
• Overwelding
• Reject, rework and scrap rates
• Post-weld grinding of spatter and excess weld metal
• Labor overtime
• Excessive arc time
Welding processes that increase deposition rates and productivity help lower the largest component of welding expenses – welding labor and overhead, which account for 60-70% of total welding costs.2
Production Inefficiencies
Achieving high deposition welds on thicker gauge materials efficiently is a complicated process. While it is possible to achieve high deposition using .045in. (1.2mm), .052in. (1.32mm) and 1/16in. (1.6mm) solid and metal-cored wires, many welders have trouble surpassing the 12 to 15lb/hr (5.4 to 6.8kg/hr) threshold.After conducting a series of in-house tests, Lincoln Electric’s research and development team found several challenges welders can encounter when utilizing either constant voltage (CV) or pulsed GMAW for high deposition welds. Mainly, welders can’t just turn up the wire feed speed to get the deposition they want without affecting welding quality.
In addition to being difficult to manage for even highly skilled welders, the arc cone that results is very narrow and produces a deep, spiked shaped penetration profile that increases the risk of plasma-induced defects. The weld puddle collapses on the shielding gas and traps it deep inside the weld. These types of discontinuities, evident through non-destructive testing, can add major costs associated with non-productive rework.
Adopting New Technologies
Most manufacturers understand the importance of innovation. Execution, on the other hand, is where most struggle. According to a Boston Consulting Group survey, nearly 90% of manufacturing leaders regard adopting Industry 4.0 technologies (such as automation) as a way to improve productivity, but only about one in four said they could see opportunities to use these advances to build revenue streams. Respondents cited defining a strategy as the biggest challenge in adoption efforts, followed closely by rethinking their organization and processes.3 Having the right skills and talent to implement new technology is also a critical factor.
Operations should closely consider the capabilities of their current workforce, the ease of adoption and whether additional training is needed for a more complete cost benefit analysis.
How Twin-Wire Welding Works
Unlike tandem welding, which requires two separate equipment configurations, twin-wire welding utilizes two smaller-diameter wires with a single power source, feeder, gun liner and contact tip. The setup feeds two wires through a single torch and uses a special output waveform to produce a “liquid bridge” that creates a single, large weld droplet and arc cone optimized for making bigger welds. The special output waveform increases arc stability and lowers spatter on large welds. This makes it
more forgiving than other high deposition processes because the operator does not have the challenge of controlling a small focused arc with a large weld puddle.
Ideal Applications
Twin-wire welding is suitable for a wide variety of heavy fabrication manufacturing, and has potential to continue to expand and be adapted to other applications.It is ideally suited for welding in flat and horizontal positions.
HyperFill Advantages
• Greater Comfort and Control • Higher Usable Deposition Rates
• Lower Fume Generation • Return on Investment
Greater Comfort and Control
Because HyperFill closely mirrors the single-wire GMAW process, welders do not have to change their behavior patterns or learn new techniques. The wire orientation does not affect arc characteristics, due to the creation of the single droplet arc cone. With HyperFill, the energy is more evenly spread over a wider area, which makes it easier to complete large welds. This makes it more comfortable and seamless for both semi-automatic welders and robotic technicians to pick up and implement into their processes.Return on Investment
Greater speeds, higher-quality welds and reduced scrap contribute to a quick return on investment. Both the semi-automatic and robotic HyperFill processes can help eliminate the need for complex, costly tandem welding systems. In addition, the consistent quality and repeatability encourage high part throughput.The ROI continues to pay dividends when you consider the ease of use factor, which helps welders of various skill levels to achieve a quality weld. Because of ease of use and high adoption rates by operators, no extensive retraining is required, which provides additional cost savings.
Conclusion
In a competitive environment, operations should closely consider any solution or process that can help them position their current workforce for improved productivity and labor savings. Along these lines, applications that demand large-sized welds represent the greatest potential for cost reduction. Making the decision to adopt new equipment and practices can appear overwhelming at first glance. However, manufacturers should look for solutions that are aligned with the skill level of their workers to make the process as pain-free as possible. Offering low system complexity and a seamless process for welders of all skill levels is where HyperFill excels. To learn how easily HyperFill can be integrated into your specific operation, you should consult with a process expert from Lincoln Electric. As a producer of the industry’s most advanced waveform technologies, consumables and automated solutions, we not only bring extensive welding expertise, but in-depth knowledge in fabrication and general manufacturing applications to the table.
By working closely with you to understand your needs for increased productivity, we can recommend the right system (whether semiautomatic or robotic) for your specific application. From better welding process capabilities to improved robotic technologies, advanced welding solutions like HyperFill provide manufacturers with a way to confront production challenges by making bigger welds faster and easier than previously thought possible.