Complete Workspace Solutions for Welding Fume Control
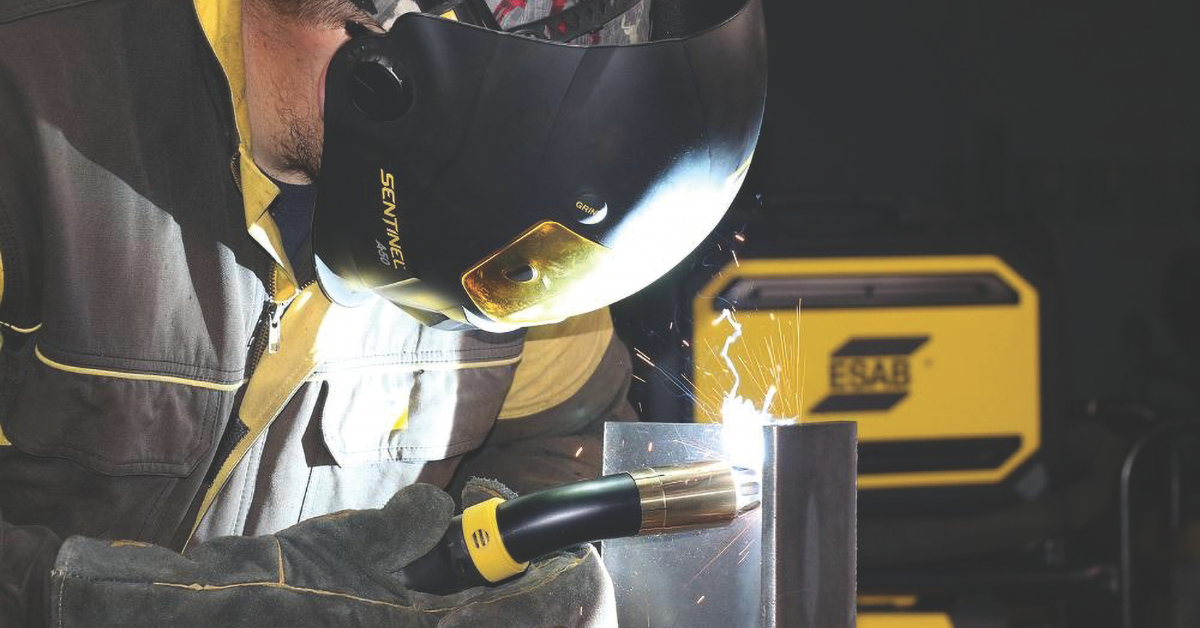
Australia has joined leading countries to now have some of the lowest, permitted workplace welding fume exposure rates in the world. Welding fumes are a complex mixture of hazardous chemicals produced during welding.
Workers undertaking welding processes are at risk of exposure to welding fumes. However, other people in the workplace may also be exposed to welding fumes. Under the workplace exposure standard workers must not be exposed to levels of total welding fumes greater than 1mg per cubic metre of air, measured over an eight-hour day, based on a five-day working week.
A powered air purifying respirator (PAPR) unit alone may not meet this benchmark. PAPRs can protect individual workers, but welding fumes can still permeate the workplace putting other workers at risk.
A suite of measures is needed to achieve optimal worker protection, site-wide. This starts with a detailed assessment of the workplace. A custom solution can then be applied to minimise welding fume exposure for all individuals in the workplace.
Seven Steps for Comprehensive Welding Fume Control in the Workplace:
1. Wearing Personal Protective EquipmentA secure, PAPR such as the ESAB Sentinel A60 Air helmet filters hazardous welding fumes for the worker during welding. Portable and back-mounted, the respirator connects seamlessly to the helmet.
Note: Fumes can still be inhaled by nearby workers not wearing PPE.
2. Mobile Fume Extraction at the source
Removing between 85% to 95% of welding fumes at the source, mobile fume extractors activate automatically when welding starts. The ESAB range includes TBi Fume MIG guns connected to the ESAB CarryVac 3 portable fume extractor with a 99% filter efficiency.
Note: On-gun fume control works most effectively in environments with poor ventilation.
3.Hooded Capture Vacuum Carts
The mobile OrigoVac Cart W3 can be wheeled around the workshop, capturing welding fume in light to medium applications. The fume extraction rate is lower than on-gun fume extraction. However, the unit is still an efficient method for capturing fumes in the work area, as long as the hood is positioned close to the welding source. The units are best suited to capturing fume over a smaller weld area, between 300mm x 300mm in size, and being used on repetitive production jobs rather than long weld seams.
Note: Hood movement and arm angle must be correct for effective use.
4. Workspace Air Flow Ventilation
Proper ventilation is vital to moving welding fumes away from the work area. This can include ventilation systems as well as simple measures such as opening roller doors or windows. Workplace air quality should be checked on a regular basis using a monitor.
5. Attention to Base Metals
The right base metal preparation can help to reduce harmful elements like rust, dirt, paint, galvanised surfaces and other coatings that may contribute to the generation of higher levels of welding fume.
6. Appropriate to Base Metals
The welding wire you choose is important. Some MIG and Flux Cored welding wires/rods can significantly reduce welding fume levels. Select specially formulated low fume, filler metal options to minimise welding fume generation.
7. Lower Shielding Gas Oxidation
MIG and FCAW shielding gases can reduce oxidation levels by minimising components like carbon dioxide and oxygen. This can reduce fume levels by up to 30%, while preserving penetration and user appeal.
Paul Morgan, National Accounts Representative SPAC at CIGWELD - ESAB, says protection from welding fume requires comprehensive solutions for the entire workplace. “Welding fume control relies on more than personal protection. It takes fume extraction at source, clean steel, the right filler metals and good workplace ventilation. All the elements need to be in place to achieve success.”
Ask your Blackwoods Technical Welding and Abrasives Specialist for the best solution for your business. Our specialists can support you with advice on product selection and implementation.