Applying the Hierarchy of Safety Controls with Blackwoods
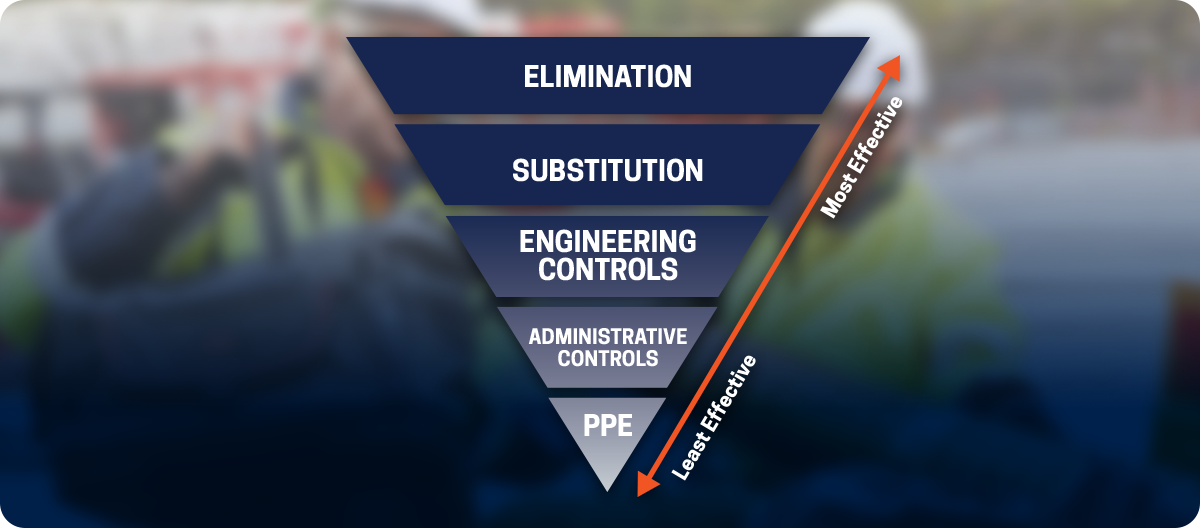
Good risk management starts with identifying hazards in the workplace, determining the level of harm they could cause and taking steps to reduce the risks they present. The hierarchy of safety controls provides a framework to help employers make these decisions.
Here are some tips for implementing the hierarchy - and how Blackwoods can help with safety solutions tailored to individual workplaces across a range of industries.
The elements of the hierarchy of safety controls
The five levels of the hierarchy are:
- Elimination of the hazard – this is top level control as removing the hazard altogether eliminates any risk that comes with it.
- Substitution – since it’s not always possible to eliminate a hazard, the next best thing is to replace it with something safer.
- Engineering controls – this involves physical changes to the working environment to either isolate the hazard or reduce the level of exposure.
- Administrative controls – such as training, new processes and procedures, rotation of staff.
- Personal Protective Equipment (PPE) – the use of PPE (e.g. helmets, gloves, hazmat suits) becomes an essential measure where the risk cannot be controlled sufficiently through higher steps in the hierarchy.
When it comes to making decisions about hazards and risks, it’s not necessarily a matter of using one level or another. The solution might involve a combination of two or more levels to create a robust and effective system for managing risk and improving health and safety.
Implementing the hierarchy of safety controls
The onus is on employers to be proactive in reducing risks and keeping workers as safe as possible. This is important not only to meet compliance and other legal requirements, but to help reduce the risk of costly insurance claims, reputational damage and lost productivity.
Here are five ways to implement safety controls in the workplace:
- Risk assessment
Conduct a thorough risk assessment of the workplace, starting with identification of hazards and determining the degree of harm they could cause. The key here is not to come up with unlikely scenarios but to identify hazards likely to cause a significant level of harm.
- Focus on the top tiers of safety
Make hazard elimination the goal where possible, since this offers the greatest protection. But if this isn’t possible, consider how to implement a substitution. Some examples include:
- Replacing flammable lubricating or cleaning products with non-flammable versions that are equally effective (such as CRC NF 5.56), in order to reduce fire risk.
- Substituting inadequate coverings on slippery surfaces with high-quality ones to reduce the risk of accidents. Our article on reducing slips, trips and falls provides examples.
- Invest in effective engineering controls
Where elimination or substitution are not possible, modifying the workplace environment can reduce exposure to hazards. Here are some examples:
- Implementing barrier systems to separate people, plant and equipment, and vehicles.
- Welding fume controls to reduce exposure to welding fumes – such as extraction products that capture welding fumes at the source and remove them.
- Dust suppression systems to reduce the risk of breathing in minute hazardous particles such as silica dust.
- Develop clear administrative controls
Workers should not only be trained in how to do their job, but also in recognising hazards and following safe practices. It’s important to develop sound safety processes and procedures at the management level, and to communicate these effectively across the worksite – e.g. through safety signage.
- Provide suitable PPE
PPE is always an important component of workplace safety solutions. But in some cases, it’s a critical first line of protection. For example, a study of welders across Australia showed that the most effective solution for reducing welders’ personal exposure was a welding helmet with a Powered Air Purifying Respirator (PAPR).
Taking an integrated approach to developing solutions
Assessing hazards and risks then implementing safety controls can be challenging. The right solution for each workplace depends on the particular industry, business operations, environment and hazards.
Blackwoods Category Manager - Workplace Safety Darren Gallagher says the Blackwoods Assess, Inform and Equip approach can help employers implement a full solution. “Utilising our knowledge and experience across industrial, engineering, and safety products, and supported by our technical specialist teams, we can deliver more effective solutions using an integrated approach across the different levels of control,” he says. “Making your business safe and protecting your people is about much more than just PPE.”
Get in touch to find out how Blackwoods can support employers in optimising workplace safety.
Related Articles
Our Integrated Approach to Safety |
3M's Hearing Protection Test is Fit For Purpose |
Measure Welding Fume in Your Workshop |
Blackwoods and Dixon team up with CPB Contractors to Fight Silica Dust |