3M Powered Air Purifying Respirators
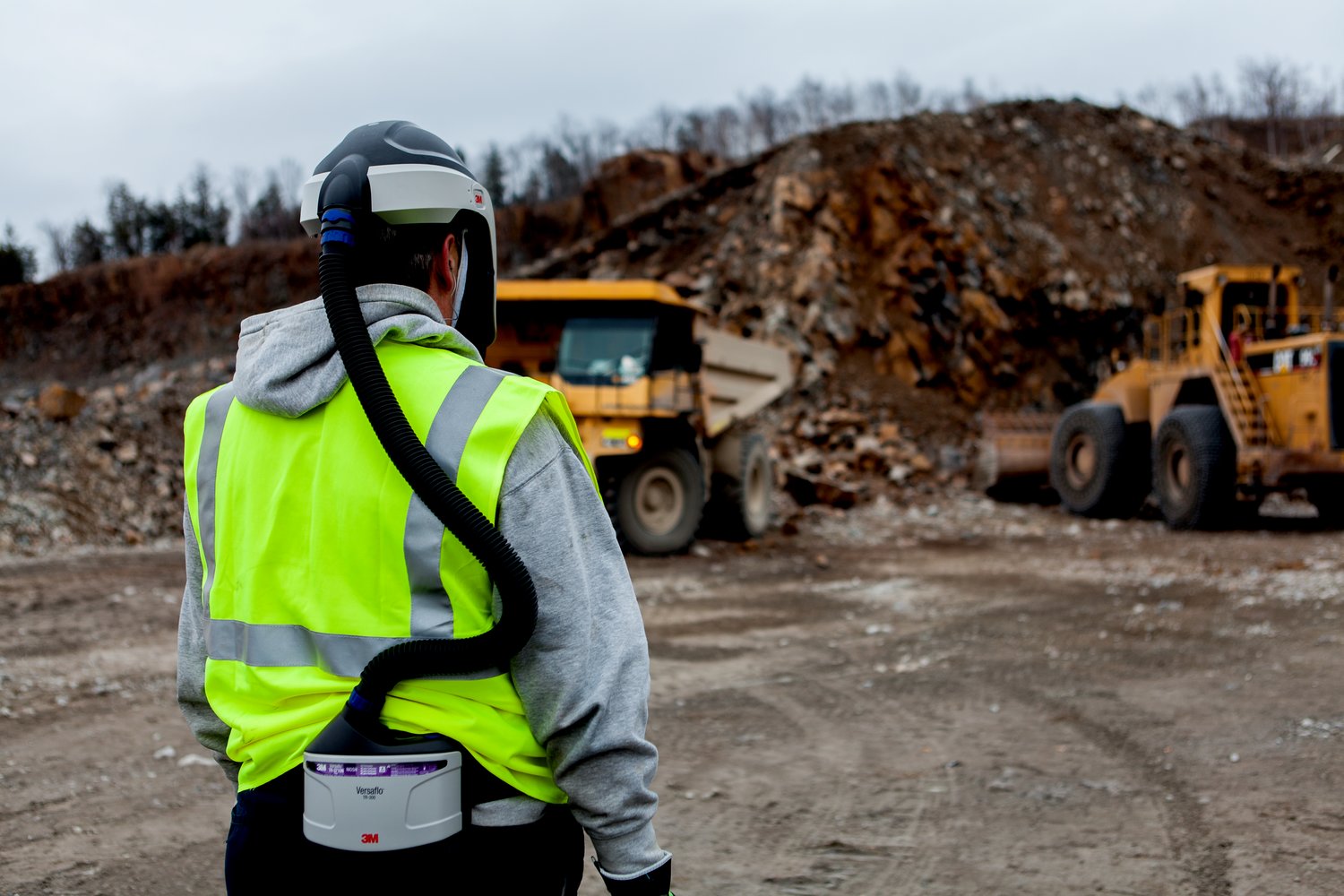
Powered Air Purifying respirators (PAPRs); include a blower that draws contaminated air through filter/s to remove
contaminants, supplying purified air to the user wearing either an open head top (loose fitting hood) or tight-fitting face piece.
Like full and half face masks, PAPRs are also available in ready-packs to simplify the respirator selection process.
3M offers a range of ready-to-go PAPR kits:
• Full face pieces for asbestos and dust applications
• Helmets and face shields ideal for many industrial applications, mining, construction etc.
The benefits of a PAPR are:
• Protection factors up to 100+, based on the head top and filter/cartridge being used
• Good option if using for long periods by reducing the weight of a filter carried on a face mask
• Helps reduce user fatigue with air moving around the head and face cooling the wearer
• Available with a wide range of hoods and head tops
• PAPR combinations that rely upon positive pressure air flow with a loose-fitting head top do not require fit testing.
These features make PAPRs ideal for industries such as; asbestos removal, pharmaceutical manufacture, smelters, waste control, land remediation, welding and agriculture. With any negative pressure or PAPR RPE the selection and use of the correct filter for the contaminant/hazard is crucial. Filters are typically designed to handle particulates, gas/vapour or a combination of both particulate and gas
The life of a gas cartridge is dependent upon the temperature, humidity, concentration and type of contaminant, the class of filter and the selected flow rate of blower. Filters should be replaced on a regular basis in accordance with an established filter replacement schedule identified in the initial risk assessment. AS/NZS 1716: 2012 recommends discarding your filter when any one of the following conditions exists:
• The particulate filter becomes difficult to breathe through
• Calculated breakthrough of gas occurs according to the filter replacement schedule identified during the risk assessment
• 6 months have passed since sealed gas/vapour filter package has been opened (if expected breakthrough hasn’t occurred earlier)
• The expiry date on the filter has passed.
In some instances, depending on the type of chemical hazard, filters must be changed out after each shift.
If filters are to be re-used they should be stored in a sealed plastic bag or box.
Filter classifications: Particulate Filters are classified as P1, P2 or P3:
• P1 filters suitable for mechanically generated particles
• P2 filters suitable for mechanical & thermally generated particles
• P3 filters suitable for mechanical, thermally generated particles & highly toxic
Gas filters are rated Class 1, Class 2 or Class 3 according to their capacity to capture and hold certain gas/vapours
The classification for gas & vapour filters is based on the groups of gases they are designed to be most effective against.
Filters have colour-coded labels for easy identification of the different group
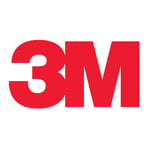